Lee Beard, a renowned crew chief who has won the NHRA World championship and is in the Hall of Fame, has maintained his presence in the drag racing community over the past few seasons by providing consulting services to multiple NHRA fuel teams.
Beard is renowned for collaborating closely with manufacturers and engineers to create cutting-edge goods that provided the teams he worked with a competitive edge in terms of performance. Powder Forged Connecting Rods
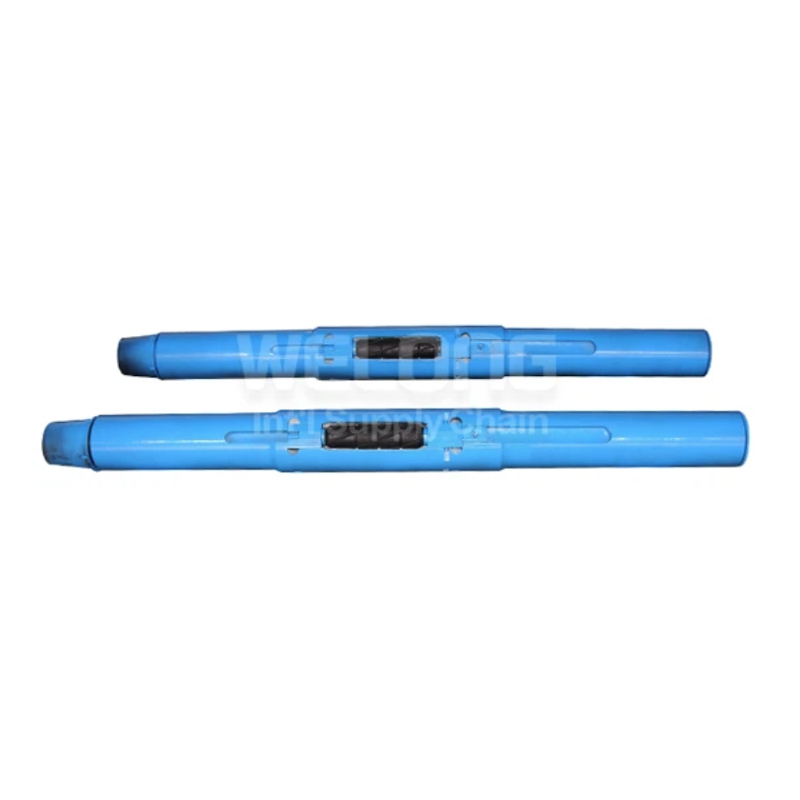
Currently, Beard is a consultant and spokesperson for AWA Forged Composites. AWA Forged Composites consists of a team of present and past aerospace engineers.
AWA's consortium consists of engineers specializing in mechanical, chemical, computational fluid dynamics, electrical, and material sciences. AWA is now advancing its research and implementation of replacing metals previously used in the aerospace sector by creating highly robust and long-lasting components from its composites.
"I have been collaborating with AWA Forged Composites for approximately five years," Beard said. "I was the pioneer in racing by being the first person to use carbon fiber for the rear wing, front wing, body, injector hat, and brakes on a dragster."
Upon Beard's introduction of the carbon fiber rear wing in 1985, he faced a significant lack of acceptance and enthusiasm.
"The material was not well-known to most people, unless they were avid followers of IndyCar racing, a group that many drag racers are not a part of," Beard said. "Upon my arrival with this item, there was a significant amount of doubt, numerous individuals expressing negative opinions, and substantial opposition to granting me permission to operate that division."
The wings of the era incorporated cutting-edge aircraft technology, with an aluminum skin and an aluminum spar structure, which were assembled to form the wing.
"A significant number of racers expressed concerns about the potential failure, crash, and high cost of the carbon fiber rear wing,” Beard said. “The resistance stems from a lack of comprehension of the product's quality, strength, and overall essence.
The depiction of the carbon fiber rear wing underwent a full transformation as time progressed.
"Five years later, carbon fiber wings became ubiquitous," Beard said. “There are currently carbon fiber wings in operation that have been in use for 20 years. The devices must undergo recertification; however, I am uncertain whether this occurs annually or biennially. The opposition I encountered when dealing with cutting-edge carbon fiber goods is comparable to the challenges faced by Bryan Gill, the chief technical officer for AWA Forged Composites, in working with forged composite materials.
“However, in recent years, there has been thorough testing conducted on his materials. This testing includes finite stress analysis (FEA), programs, destructive testing on every component, as well as spintron and dyno testing on the valve train. Rest assured; I would not be part of this team if I believed this product would fail.”
Beard commended the people he has been collaborating with at AWA Composites for instilling in him a robust conviction in the organization.
"These individuals are current and former aerospace engineers who must construct products according to specifications that are unknown to anyone in the drag racing community," Beard said. "When entering the world of motorsports, failure is not an option, and I assure you that this product will not disappoint."
AWA Forged Components, as stated on its website AWAComposites.com, is a company consisting of a team of highly skilled mechanical, electrical, and chemical engineers from the aerospace and automotive sectors. They collaborate to produce top-quality car components that are considered the best in the market.
Although numerous manufacturers provide carbon fiber choices for aesthetic reasons, AWA Forged Components acknowledge that the advantages of composite materials go beyond just stylishness. They possess superior rigidity, durability, and reduced weight compared to existing metallic materials. Extensive research and development efforts have led to the creation of multiple patent-pending designs, trademarks, and groundbreaking automobile components.
AWA is adamant they place the highest priority on supporting our communities. Likewise, they are committed to fostering the growth of young, ambitious engineers who have a keen interest in pursuing careers in the automotive or allied sectors, by offering internship opportunities.
Manufacturers are obligated to significantly enhance their vehicle performance and fuel efficiency in the upcoming years, and AWA believes they will depend on technology to achieve this. We are at the forefront of developing composite technology, surpassing even the largest companies in the industry. Our innovations are setting new performance benchmarks that will be permanently documented in the history of automotive and mobility.
"Top Fuel is the sector that exerts the highest demands on connecting rods when considering cylinder pressure," Gil said. "Therefore, our primary objective was to overcome the most significant and challenging obstacle, symbolized by the 800-pound gorilla. We believed that achieving success in this endeavor would have a domino effect, causing the resolution of all subsequent challenges."
Beard encountered similar skepticism when he introduced the carbon fiber rear wing. AWA Forged Composites has faced the same doubts regarding their forged composite products.
"A group of my peers and I decided to enhance our retirement income by developing applications that could be beneficial in the field of motorsports," Gill said. "We primarily specialize in applications within the aerospace industry and work as contractors for the private sector and the Department of Defense.
“We examined materials that had been declassified from the military and repurposed their applications, focusing specifically on their composition, fiber alignment, and other relevant factors. We were well-acquainted with the military, which used a concept known as "de-weighting." It refers to the process of examining and revisiting various designs, functionalities, and operational tasks of specific components, intending to identify methods to enhance their strength and reduce their weight. That is the objective we have been assigned to accomplish for the past three decades.
Beard, in his role as a crew chief and team manager, has achieved a remarkable total of 55 victories in NHRA national events. These wins have been accomplished with the assistance of 14 different drivers, competing in both the Top Fuel and Funny Car categories. Seven of those drivers achieved their first victory in a national race. He has a strong passion for sports and AWA Forged Composites provides him with the chance to continue actively engaged in that field.
One of the main advantages of AWA Forged Components is the significant reduction in weight and increased strength of its products.
"The company has more than four Sr. engineers who have pooled their expertise in computational fluid dynamics, electrical engineering, mechanical and aerospace engineering. These diverse disciplines have been combined to develop highly distinctive components," Gill said. “We have partnered with a highly proficient manufacturing entity and are currently seeking a distribution network.
As an example, a typical valve spring retention made of titanium weighs 23.1 grams, while a retainer built of forged composites weighs 5.7 grams. It weighs one-fourth as much and is significantly stronger than the titanium one.
AWA Forged Components offers a variety of goods, including the valve spring retainer.
The components include Composite Push Rods, Composite Connecting Rods, Composite Pistons, Composite Wrist Pins, Composite Lifters, and Kiptanium™ Rod Bolts.
Gill said, “When we replace parts made of steel, which have a density of approximately 7.4 grams per cubic centimeter squared, with materials that have a density starting from 0.8-1.4 per cubic centimeter squared, we are aligning with the objectives of the military and aerospace industry. We were aware that simply replacing materials could yield significant benefits." We examined the optimization of carbon technology's design and successfully improved it by reinforcing only the necessary areas if that is clear to you.
Immerse yourself in the realm of drag racing. (Serving as a starting point for the technical proof of concept, without necessarily being a viable business model)
"It is imperative to establish a starting point," Gill said. "You are interested in a timed event like drag racing, where two vehicles accelerate a mass. This event represents the physics equations we aim to highlight, as any acceleration over a specific distance involves fundamental principles of physics." We anticipated that our technology would exhibit the greatest disparity compared to the traditional methods they have previously employed.
Beard announced that the AWA Forged Components be present at Performance Racing Industry Show Dec. 7-9 at the Indiana Convention Center & Lucas Oil Stadium in Indianapolis. AWA will be in booth 1537 and manufacturers and racers are encouraged to come by and look at this cutting-edge technology showcased in AWA’s products.
"We have conducted a comprehensive series of tests with different spintron operators, dyno operators, and extensive analytical testing. Additionally, we have developed highly advanced and intricate software." We don’t have a question of if it will work, but rather how well it works, and how much we can keep the expenses down. Those are likely the two most significant questions we will encounter.
"The 2023 PRI Show serves as our debut event. After eight years we hereby assert our position as the preeminent wrist pin manufacturer worldwide, offering the finest rocker system and valve train components available. We are prepared. We have completed numerous tests and are now ready to present ourselves as a disruptive force in the industry. Our goal is not merely to compete with existing technology, but to revolutionize it and pave the way for new and innovative advancements. This technology will revolutionize the current state of affairs.
"I possess an equivalent level of assurance in the product that they have created," Beard said. "I repeatedly conducted tests using the carbon fiber rear wing, and despite my doubts, I was not completely convinced." The engineers who were engaged in the development of that rear wing exhibited great optimism, and to everyone's surprise, it subsequently dominated the industry. AWA is encountering the same level of doubt and disbelief as I did when introducing carbon fiber technology, but now it is facing it with forged composite technology.
Gill succinctly elucidated the robustness of AWA-forged composites.
"We have a higher stiffness than H-11 tool steel, and, in terms of volume, we are approximately as strong as steel and significantly lighter than aluminum," Gill said. "To clarify, a few years ago at PRI, we encountered a customer who visited our booth. He mentioned that he used to work as an engineer for a helicopter company. His specific role was to upgrade the helicopters by replacing their rotor blades with composite ones."
He desired to experiment with composite rotor blades as a replacement for the aluminum blades. The team diligently examined their records as these blades were surpassing the existing ones in durability. When the blades reached the 10-year mark, there was apprehension among the DOD industry, as they anticipated their inevitable failure.
After disassembling and thoroughly examining them, doing stress analysis and destructive testing, it was determined that the composite material exhibited no signs of fatigue. Many of the helicopters are still operating with the original rotor blades they were equipped with initially.
Beard highlighted another advantage of the forged composite material.
"Despite the higher initial cost of the forged composite material, it is more economically efficient due to its significantly longer lifespan," Beard said.
Gill briefly elaborated on the factors that led AWA Composites to its current state.
"Our initial goal was not to compete with other companies that were producing similar products," Gill said. "Initially, we formed as a consortium of technology experts who utilized our collective talents and specialized skill sets to create distinct and innovative components for the industry." As a technological company, our intellectual property (IP) is essentially our most valuable asset.
"I want to emphasize that we offer private label services, as well as options for leasing and outright purchasing of our intellectual property." We do not intend to exhibit arrogance or make claims of displaced companies, thereby preventing them from providing sustenance for their families. We assert that we possess advanced technology since both technology and its capabilities have progressed significantly. Consequently, certain aspects warrant careful examination. If you find that attractive and believe there is a potential match for your corporation, then consider examining us. Otherwise, we all have to earn a livelihood, which will compel us to engage in undesirable economic ventures.
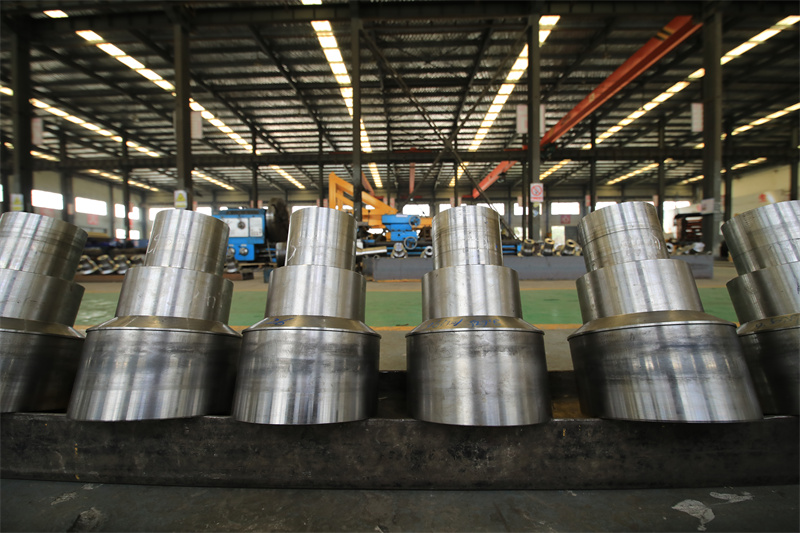
Connecting Rod Forging "If anyone believes they can use a steel or aluminum rocker to rival ours, we invite them to participate in a spintron showdown or a dyno showdown. However, it is highly unlikely that they will achieve the same level of performance."