Dienes Corp. USA in Spencer is wholly owned by the Dienes family in Germany, which also owns the original plant called Dienes Werke, dating to 1913. With a U.S. presence since 1954, the company has 40 employees in Spencer, and 575 employees worldwide, with other locations in Germany, Poland, Hungary and Malaysia. The Spencer facility serves customers in the United States, Canada and Mexico. Dienes Corp. USA President and chief executive officer William Shea, a Charlton resident, joined the business in 1987, working his way up the ranks from manufacturing manager and general manager. Dienes designs, manufactures and distributes products from knives to automatic positioning tools.
How would you briefly summarize what Dienes USA produces? Cardboard Slitter Knife
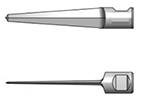
"We’re a little bit diverse. The strongest part of our business is in circular slitting, both in the manufacture of circular slitting knives, as well as equipment that positions the knives. It uses microprocessors to position the knives in the proper locations. Part of the company specializes in slitting knives and metals, stainless steels, steels up to a quarter-inch thick. Dienes Werke specializes in the slitting of paper films and foils and also the manufacture of some valves for the compressor industry. The valves are used for air compressors and refrigeration compressors."
What markets do you serve? What do you make?
"It’s a variety. The biggest one is what we call the converting market, where people will take a large roll of material and either laminate it, or put sticky materials on it, print on it, and cut it into different widths. So they unroll a master roll and they will go through a process and then slit it into narrower widths, and rewind it into narrow rolls. The most obvious one people would recognize would be masking tape, where the paper will come off of one end, apply adhesive to the paper, and then slit it into narrow widths, and then rewind them onto small rolls. One that people never see is paper being made. The roll might be made in a paper mill, rolled into a giant roll — 14 or 15 feet in diameter, and 30 or 40 feet long. Then it goes into an unwind at very high speeds — the paper may be coming through at 70 or 80 mph. Where they cut the paper is where we come in. We build the structure that holds the circular knife holders and position them to achieve the widths, and hold the material to be rewound. We also manufacture circular knives for slitting steel. We only do the knives in that market. They are ultra-precision knives that are held to very close thickness tolerances of plus or minus 20-millionths of an inch. We service the market with a variety of circular knives - 200 different styles that we stock. The customer calls and we can ship same day. Or they may want a special set that we don’t stock, and those take eight to 10 weeks to manufacture."
I imagine you would have to have a lot of safety precautions here?
"We’re very proud of our safety record. Very rarely do we have any lost time accidents. We have a vibrant safety committee that inspects the plant on a regular basis. Members of the safety committee are rotated so every employee has a responsibility to appear or serve. They have the authority to shut down an operation if they deem it unsafe."
Can you explain how robotics are used versus manual processes?
"In the manual setup, an operator will slide knives along a shaft, lock them onto it using various techniques, and take a top knife and line it up to a bottom knife, so that the two act together as a rotary pair of scissors. Each cut might take five to 10 minutes. If a customer has a machine that has 30 cuts, you can imagine they’d be in there for several hours. We’ve built equipment that will actually do that change for the operator inside of five or six seconds, so that the machine does not stand idle, and produces whatever value they are doing to the operation constantly instead of having down time. Using a robotics type of setup, we actually place those knives on the shafts or the holders along a crossbeam using the latest technology on placing them in the proper location, which gives them a tighter tolerance on their resulting slit. We sell both."
Do you have plans to expand or make changes?
"No. I don’t plan to expand at this point, but we’re investing in new equipment. One will be a manufacturing cell that will be loading and unloading the machine using a robot, and we hope to have that run 24/7. We’re looking to automate more. We’ve done the same thing in Germany. We have automated manufacturing cells already."
What is your biggest challenge as a CEO?
"It’s to stay ahead of the market on technology. We’re introducing two new products next month at a Chicago area exhibition center. One is an electronic knife holder for positioning the knives relative to the female (bottom) knife and also monitoring vibrations. So we are pushing the limits on technology. We are also introducing a product for positioning knives at the end of a printing press."
What qualities do you look for in an employee?
"No. 1 is attitude. No. 2 — abilities. We need team players. They are more important to us than superstars."
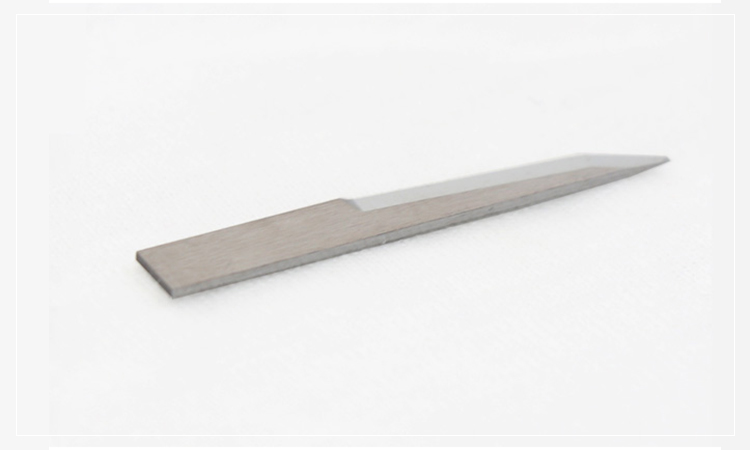
Circle Knife Compiled by correspondent Susan Gonsalves